近年来,我国新能源行业跨越式发展,作为行业重要组成部分的光伏组件制造也迎来了广阔的发展空间,随之带动了组件制造过程中智能物流的快速升级。
该项目用户是中国民营企业500强,智慧能源解决方案提供商,其位于江苏盐城基地主要负责电池片生产。光伏电池片生产要求24小时不间断作业,对于搬运精度和效率都有着较高要求,传统人工作业严重制约企业快速发展。
国自光伏电池片智能搬运系统,使用超过百台AGV及机械臂、输送线、缓存WIP等集成设备,实现从制绒到丝网、包装的空满花篮智能流转,同时物流系统兼容机台耗材更换、维修检修、技改升级等任务,助力用户实现全厂生产物流智能化、自动化,大幅提高生产效率。该项目高效融合智能物料管理系统(MCS)和智能调度系统(RCS),进行算法优化匹配,通过最优需求产生、任务管理、路径规划,实现最优效率。
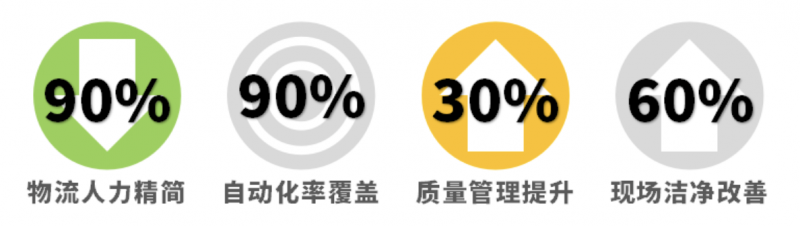
该项目属于全人工老厂智能化改造项目,原生产工艺设备规划时并未考虑自动物流生产设计,导致大量设备上下料机台的传输轨道高度、中心距以及花篮形态各异,无法使用常规标准型AGV直接进行搬运,给生产物流自动化带来很大难度。国自采用“AGV+”模式,让AGV与配套集成工业机器人、变轨机构等定制非标自动化设备协同作业,实现花篮传输姿态、空间位置的转换,从而将所有的对接口统一标准,实现全厂自动化,大幅提高生产效率。作为改造项目,用户要求实施过程不影响正常生产,国自在项目交付过程中,实现“边生产边改造”,保障产能不受影响。
由于原生产布局规划按人工作业模式设计,导致AGV运行物流通道宽度不足,部分通道只能允许单AGV通行且人车混行,给高节拍、大流量的搬运要求带来了极大的挑战。国自通过对现场地图路线、缓存位设计深度研究分析,提前进行数据仿真,采用大小循环嵌套智能调度模式,克服通道狭窄困难,消除物流瓶颈,使AGV快速上线投运并大幅提高生产效率。
现场通道宽度不足,对AGV运行的安全防护造成了较大困难,对AGV与AGV之间、AGV与设备之间、AGV与通道边缘之间、AGV与人员之间的安全距离都提出了较高的要求。国自ANTS系列机器人采用高精度激光SLAM、视觉定位技术,全面保障车体运行安全,现场设备间最小间距仅为5cm,仍可以高速稳定运行。同时,通过配置多种安全传感器,并根据不同路段配置不同交通安全策略,调度后台实时监控车辆状态,从现场硬件到后台软件,多管齐下保障现场的安全运行。
国自智能光伏生产平台系统与用户现场生产设备机台自动对接、信息交互,实现生产搬运任务自动下发,无需人工干预。该系统具备物料全流程追踪管理功能,生产异常时支持自动精准定位异常工序,方便快速排查问题,助力用户打造信息化、数字化、智能化工厂。
目前,我国已经成为全球光伏行业发展的标杆。随着全球光伏市场的快速发展,光伏制造工艺的不断提升,越来越多的生产环节需要依赖自动化、智能化,智能物流必将成为制造环节中不可或缺的一部分。在光伏制造行业,国自已为多家头部企业提供智能物流产品及相关解决方案,涉及多晶硅、单晶硅到电池、组件等全生产场景,涵盖多种工艺、物流要求,提供匹配场景的多元化、智能化、柔性化厂内物流解决方案,也是移动机器人行业内极少数拥有全生产环节应用案例的公司之一。智能物流机器人系统凭借信息化、自动化、智能化的优势,将有效提升光伏企业的智能制造水平,也将成为助力光伏行业产业升级的关键设备。