海通机器人-某汽车工厂项目
1、项目基本描述
客户痛点:发动机下线人工转运效率低、人工劳动强度大、负载大,转运不便。
解决方案:某汽车厂工厂项目发动机P线和Q线原为人工下线并由人工转运到总装线,工人劳动强度大,效率低。根据客户要求,海通机器人为发动机工厂实施了P线和Q线发动机自动下线及AGV智能转运项目。海通机器人以核心优化算法的调度系统作为中心,与WMS、MES、ERP、排产系统等生产管理系统无缝对接,根据车间环境布局,用18台AGV为基础,打造了全新的柔性发动机转运线,可适用多车型混合生产,灵活性高,柔性高,可维护性高。采用最新的优化调度算法,与生产管理系统实现无缝对接,真正实现了发动机智能物流,提升输送效率,减少现场物料缓存,实现JIT生产。
2、项目创新性
项目车型选用最新的整车五重安全防护设计,采用了多项行业首创安全设计,并率先在行业内采用嵌入式控制平台,在单车控制器内集成优化算法,使得单车本体具有个体智能。顺利通过该集团严格评审和TUV安全认证。
3、行业影响力
该项目获得该品牌汽车德国总部的特别贡献奖,其后海通机器人还陆续实施了该汽车总装工厂AGV智能物流项目。
新松-T公司底盘合装AGV及前、后悬转运AGV系统项目
1、项目基本描述
为配合T公司持续推动新能源汽车领域科技创新及极速扩大产能需求,受其委托,新松公司承接其底盘合装及前、后悬转运共计三条生产线的AGV系统布置任务,秉承着T公司超级工厂项目当年建厂当年量产的“T公司速度”,同时还需要满足T公司的高标准要求,高效生产需求。
2、项目创新性
- 新项目中,新松不断优化和创新移动机器人软硬件技术,帮助T公司将原有90JPH生产节拍提高到103JPH(每小时有103台下线),一举成为全球最快的汽车生产线。
- 新松提供了一款全新研发的双举升全方位移动机器人系统,用于解决其物料运输的痛点,同时通过优化运输路线,合理布置转接站点,大大提高机器人的运输效率。
- 通过软件调度的不断优化和逻辑更新规划,满足其原有较复杂的输送多样性需求。
3、行业影响力
T公司基于与新松移动机器人产品性能优势和服务优势,再次选择大批量复购。
贯穿T公司汽车生产全生命周期,新松移动机器人已经实现了从合装,前后悬分装再到电池车间的全流程覆盖。
海康机器人-南京长安整厂智能化项目
1、项目基本描述
南京长安环保搬迁(置换升级)项目,于2022年10月顺利通过SOP。海康机器人助力南京长安环保搬迁(置换升级)项目智能化建设,利用移动机器人建设各生产线,包括内饰、完成、电池pack、前后桥分装、仪表、前端模块等环节。移动机器人实现工艺物流的无人化配送,包含大件货到人,以及利用CTU的小件仓储及自动分拣。项目整体覆盖总装、冲压、焊装、电池车间,共计投入400余台移动机器人。
2、项目创新性
- 汽车主生产线采用AMR建设:完成内饰线采用全新定制的重载AMR替代原有的滑板线,并且内饰线AMR可实现物流同步搬运,在满足滑板线所有功能的基础上,达到生产线柔性大,节拍调整灵活的效果。
- 冲压车间全流程自动化:利用AMR、视觉读码门 、电视看板等实现空盛具补充、盛具校验、自动下线、生产线切线等全过程自动化。
- 信息数字化管理:智能仓储管理系统iWMS和机器人控制系统RCS无缝对接LMS系统,实现仓储信息和产线配送信息数字化管理,提高信息准确性和配送及时性。
- 交通管制:不同场景的AMR共线运行,在运行过程中自动进行交通管制,对人、AMR之间的流向进行管控,规避拥堵及安全隐患的同时,提高配送效率。
- 小件CTU立体库:利用CTU、机械手、3D视觉、智能读码、潜伏式AMR等产品实现小件自动拆垛入库、自动分拣、自动装车、自动配送。
- 自动拉动系统:自动补料拉动系统部署在总装车间料盒打包区,通过空箱自动触发物料配送补料任务并进行亮灯指引。整个系统实现基础数据管理、补料流程控制、终端状态监测、报表管理等功能。
- 生产信息同步:RCS与工艺设备PLC对接,实现信息流的互通,实现焊装、总装车间自动化工位的自动补料及空箱自动返空,补料过程可进行物料信息的交互校验,提高配送的准时性和准确性。
3、行业影响力
- 生产模式的变更:随着移动机器人技术的不断发展,用其建设的生产线器柔性更大、新车型切换成本更低。在汽车行业生产车型更新速度加快的当下,移动机器人生产线将变为主流。
- 智慧物流建设:南京长安项目应用了多项先进技术,包含5G、机器视觉、移动机器人、工业机器人等,打造了几乎覆盖汽车行业主机厂所有应用场景的智慧物流。
CSG华晓-某欧系高端汽车品牌路桥工厂电池PACK柔性化装配线项目
1、项目基本描述
该项目采用先进的柔性化装配理念,可实现零件集配、上件、分装、下件全流程,真正做到零件运输流、产品装配流、成品下线流“三流合一”。CSG华晓结合动力电池PACK的工艺要求,设计建造了集零件集配、物料配送、动、静态测试、成品下线于一体的柔性化装配线,并且依据人体工程学首创翻转式AGV,该型AGV可根据不同工位的不同工艺需求,自动翻转工件,节省装配人员5名,提高了15%的运转效率。
2、项目创新性
- 装配柔性化采用AGV携带装配平台和物料,形成模块化的可移动载体,替代传统的输送产线。该款AGV可实现双边30°-60°的翻转,人员操作简单,只需按下按钮,即可完成自动翻转,解决因电池包宽度过大,单人装配不方便的工艺现状,提高产线柔性化,大大节约了企业用工成本。
- 车体具有防坠落装夹机构的专利,翻转到位后自动锁紧,保证电池包倾斜状态时,人员装配的安全性,同时也可配合精定位机构,实现电池包±1mm以内的定位精度。在生产过程中,物料信息可以与AGV实时绑定,追溯可控。
- 人性化的机械结构设计和封装保护,保证人员操作时不会发生夹手,夹脚等安全问题。360°无死角安全防护+车身四周安全示廓灯,时刻保证运行过程中的人机安全。当发生故障时,AGV可以快速切换下线维修,备用AGV立马替换上线,解决传统输送线故障造成的长时间停线维修时间。
- 对于前期投入来说,也可以进行分批试点,后期线体复制也快速便捷。
3、行业影响力
CSG华晓从前期分析,方案设计,样车原形测试,安装调试,后期维保,为客户提供了一站式解决方案,使用80天,即完成42台各型AGV的设计到安装调试。项目投产后运行稳定可靠,成为行业内的明星产品,得到用户的一致好评。该产品已申获两项新型实用专利发明,两项发明专利正在实审阶段。
浙江中力-某汽车零部件企业焊接车间AGV项目
1、项目基本描述
客户介绍:该企业是一家成立于2014年的中外合资企业,主要从事汽车零部件的冲压、焊接及相应的模具、夹具设计、制造,融合了信息化、自动化生产及运输的自动化生产的一流汽车零部件制造工厂。该厂总占地面积97853平方米,设置主要产线3条,年产量20万台配套,其高质量部件受到诸多高端车企品牌的信赖。
客户痛点:生产节拍快,转运频率高;场地空间有限,线边缓存数量少;传统人工配送,效率低,强度大,准确性低;用工成本高,人员招聘培养周期长,管理难;工厂智能化转型,需柔性高效的智慧物流解决方案。
解决方案:在仓库内投入一批XPL201搬运机器人,速度高达2.5m/s,载重2吨,24小时不间断执行自动化产线送料和成品转运,实现从“人找货”、“人送货”到“货到人”、“货到仓”的智能化管理,打造工业4.0时代汽车部件生产制造智能工厂。
双车协同搬运,最大效率实现产线工位物料空满替换。产线工位完成品下线即刻有机器人自动搬运入库,同时另一台机器人快速搬运空料框至产线,承接新的完成品下线,实现生产制造过程中物流搬运的无人化作业。
应用成果:助力企业打造工业4.0时代汽车部件生产制造智能工厂,双车协同,实现生产制造过程中物流搬运的无人化作业,部署面积超5500平方米,每日总运行距离超900公里,极大提升场内货物搬运效率,削减叉车驾驶人员8人,叉车4台,年平均节省成本近百万元。
2、项目创新性
- 快速部署,产线不停产。中力机器人团队驻场全力配合,梳理业务需求,实地勘测场地,规划部署方案。部署面积超5500平方米,仅7天就可全部完成,实现了从人工叉车到机器人智能搬运的无缝切换。部署效率极高,完全不耽误产线正常生产,确保客户生产需求和正常效益。
- 高效精准自动配送,24小时不停歇。该企业场内面积大,中力搬马机器人XPL201速度高达2.5m/s,实现原料和完成品的快速转运。基于激光导航、定位导航算法等,中力搬马机器人做到复杂场景不丢失,配送准确率高达100%。根据实际产线作业需求,中力搬马机器人实现自主充电,智能调节充电时间。在生产制造高峰期,智能缩短充电时间,极大满足客户双班倒,24小时作业无限制。
- 双车协同配送,更高效更安全。创新双车协同搬运,最大效率实现产线工位物料空满替换。产线工位完成品下线即刻有机器人自动搬运入库,同时另一台机器人快速搬运空料框至产线,承接新的完成品下线。机器人匹配多重安全保障系统,人形识别AI,分级避障,多重警示,让场内作业更安全。
- 分布式集群作业,可柔性增减。去中心控制化,分布式管理,机器人完全自主控制与交互协作。基于多智能体算法的任务指派和交通协调,实现高效的任务指挥和车辆运营管理。随着客户业务量的变更,还可快速扩充机器人,且新扩容车辆无需重复学习。
- 独立管理系统,简单快速应用。中力搬马机器人采用独立的呼叫和调度系统,独立运转,无需对接客户生产系统,可快速投入运转,且成本低。
- 全周期专业服务,使用无忧。专业服务团队,解决前中后期的使用管理问题。前期专业团队部署落地。中期组织操作、保养等培训;后期 2 小时响应售后需求,定期车辆巡检。
3、行业影响力
在汽车行业首次导入2.5m/s高速版叉车AGV,20台叉车AGV协同,实现焊接线快速上下线的需求,效率方面创行业新高。独立呼叫和调度系统,无需对接客户生产系统,落地快,运行稳定,操作简单。
迈睿机器人-某动力电池组装配线项目
1、项目基本描述
该项目位于温州乐清,AGV主要应用于动力电池组装配线。该项目主要特点是对接多种自动化设备,多车型混合调度。通过对潜伏举升式AGV进行改造,满足现场多种载具在多种自动化设备上的对接及搬运,同时搭配滚筒式AGV实现料箱在输送线上的移载。AGV与自动化设备的对接,使生产更加柔性化,同时利用迈睿自研的调度算法,实现了多车型在不同自动化设备间的高效率调度,给客户带来了很好的经济效益和社会效益。
2、项目创新性
- 对接高度760mm,符合人体工学,不改变传统装配线员工的操作习惯;
- 举升行程100mm,极大满足了偏载和定位精度的要求;
- 一款AGV匹配装配线上不同电池包的生产,柔性化程度高,效率高
3、行业影响力
- 大大提高了电池包装配线的效率,替代了传统人工叉车搬运、输送线运输以及磁导航AGV运输的作业工序;
- 柔性生产,为电池包装配线首次使用二维码AGV,并做成了电池包行业的标准车。
法睿兰达-某新能源汽车总装生产主线AGV项目
1、项目基本描述
客户为国内某新能源汽车知名品牌企业,应用场景为总装生产线,以AGV替代传统滑板线转线机构,要求在极低的空间内实现滑板的转运,载荷达到8T。针对客户要求,法睿兰达开发设计一款超薄的主线AGV,车体高度不到190mm,实现8T载荷,并达到生产线的高节拍要求。
2、项目创新性
- 实现8T载荷的同时,车体极限超薄设计,整车高度小于190mm。
- 替代传统转线机构,减少设备基础及大型设备投资,缩短建设周期50%。
3、行业影响力
采用AGV实现乘用车总装生产主线的柔性化提升,一改传统机运线,免设备基础,缩短建设周期50%,开拓移动机器人在汽车制造柔性产线应用扩展。
UQI优奇-知名新能源车企济南总装工厂SPS物流项目
1、项目基本描述
知名新能源车企在济南落成新基地,该基地占地4000亩,可年产15万辆整车以及电动总成和电池等核心零部件。客户为提升济南基地总装工厂厂内物流效率,引入UQI优奇全栈式SPS物流自动化解决方案,该项目导入了75台T1000潜伏牵引机器人、14套SPS上线机构及其配套的智慧工厂云平台MES系统,以低成本改造实现总装工厂SPS物流智能化升级。通过UQI优奇的全栈式SPS物流自动化解决方案,知名新能源车企总装工厂SPS物流以潜伏牵引机器人T1000替代传统牵引车和人力,实现无人配送,这不仅能降低人力成本和牵引车数量,更能提升工厂内的安全性、物流效率及空间利用率。
2、项目创新性
- 拥有三级伸缩结构的SPS上线机构令其尺寸达到最优,占用空间达到最小,令生产线边空间利用率提升30%;
- MES智慧工厂云平台全局调度,多机协同操作,实现人员减配20-25%;
- 通过潜伏机器人T1000和SPS上线机构的配合,物流效率提升15%。
3、行业影响力
艾吉威-某合资新能源汽车AGV项目
1、项目基本描述
- 项目背景:现场人工搬运难以达到工装配合精度,无法完成整个线体的流程节拍。故导入叉车AGV自动搬运系统、库存管理系统、控制软件,与线体的PLC对接,实现自动搬运料架。
- 项目流程:搬运载具在A/B/C/D四个上下料点进行流转。A→B,C→D, D→A(B→C为输送线体 ),车型切换时需要增加D →存储区,存储区→A。存储区需要20个库位来存放更换的料架。
- 解决方案:根据现场工艺场景特殊,艾吉威全向叉取式AGV采用基于自然轮廓的激光定位与导航技术,在动态环境下末端精度可达±5mm定位精度,本项目采用5台全向叉车AGV完成搬运引擎盖从产线下料进烤炉烘烤,烘烤完搬运至产线进行上料的搬运流程(如产线跟换引擎盖型号,需叉车AGV自动更换流转料架)。
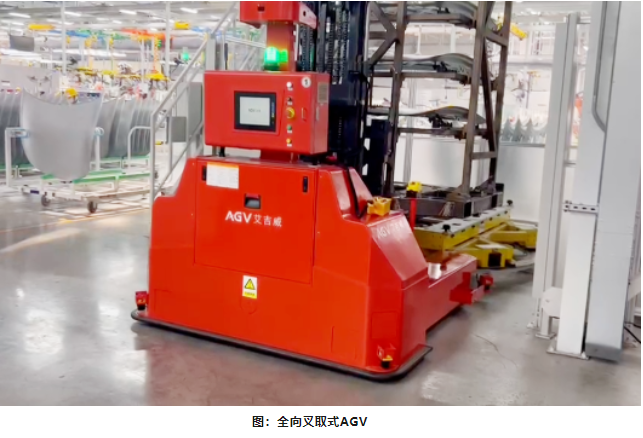
2、项目创新性
- 引擎盖搬运上下料需要叉车AGV将载具精准的放置在放货平台上,与现场机械手对接,精度要求±5mm;
- 整车生产流水线节拍快,86s完成含4个任务搬运的循环;
- 现场可用通道狭窄,常规叉车AGV无法在现场完成取放货作业。基于此种工况下,选配通道需求更小的全向叉车AGV,额定负载1000kg,堆高6m,实现2.5m的通道内全向行驶取放货。
3、行业影响力
该项目使用方为宝马在中国成立的合资公司,专注于新能源汽车领域,此项目一期的成功实施,后续将在其他工厂复制化应用,全数字驱动,智能化生产模式将在新能源汽车领域起到标杆示范作用。
舜宇贝尔-某头部车企焊装车间高速重载机舱焊接转运项目
1、项目基本描述
某头部车企为应对新能源汽车政策,焊装车间融合自适应生产理念,首次在量产生产线上实现了不限车型、不限平台,有效提高该企业生产线自动化水平,实现少人化、低成本,高效率。
2、项目创新性
- 首次以智能AGV为载体代替传统滑撬用于高节拍(60JPH)焊装线体内;
- 应用高速高精(精度±3mm,速度1m/s)重载工艺AGV,实现线内外工装智能转运;
- 采用智能AGV串接多个焊接岛可完成多车型的柔性快捷切换。
3、行业影响力
- 填补焊装产线岛内智能AGV应用空白,提供了一种全新的生产模式;
斯坦德-某新能源汽车龙头企业总装车间自动化物流项目
1、项目基本描述
某新能源头部车企导入斯坦德AMR及柔性物流方案,从而提升汽车内饰车间物料搬运及内饰总装零件的自动化配送效率。项目涉及配送工装包含多类型的专用料架、卡板箱等;同时需对接工厂早期导入的部分传统AGV设备。
2、项目创新性
- 新能源汽车行业柔性物流解决方案:大大了加快货物流转率,以灵活、柔性的智能物流方案,提高产品生产效率,大幅降低企业生产管理成本;
- 基于AMR、无人叉车多类型应用以及RIoT软件平台的整厂物流解决方案:斯坦德RIoT机器人物联网平台以智能设备和柔性物流业务为核心,通过信息融合技术、数字孪生技术实现制造场景下OICT 信息和数据的融合打通,持续帮助客户发掘更好的物流解决方案,助力智能工厂实现实时协作、数据监控、智能分析等功能;
- 多品牌AGV/AMR调度与管控方案:高效的智能机器人集群规划算法,解决集群机器人大规模调度问题,保证生产物料配送的及时性和效率,同时可兼容不同品牌的AGV/AMR。
3、行业影响力
帮助企业用智能化手段提升厂内搬运效率,项目落地后稳定运行,得到了用户的认可。
《新能源汽车行业用移动机器人(AGV/AMR)解决方案蓝皮书(2023版)》已于日前正式发布!该蓝皮书由CMR产业联盟、新战略移动机器人产业研究所主编,苏州海通机器人系统有限公司冠名发布,新松机器人自动化股份有限公司、杭州海康机器人股份有限公司、华晓精密工业(苏州)有限公司、浙江中力机械股份有限公司、浙江迈睿机器人有限公司、法睿兰达科技(武汉)有限公司、无锡优奇智能科技有限公司、宁波舜宇贝尔自动化有限公司、苏州艾吉威机器人有限公司、菜鸟物流科技、斯坦德机器人(深圳)有限公司等企业联合参编!该蓝皮书深度解析了当前新能源汽车行业移动机器人(AGV/AMR)应用现状,对行业应用现状及趋势作出研究及预判。